High Velocity Oxy Fuel (HVOF) Coatings | Overview & Services
HVOF Shock Diamonds
Carbide Surfacing of Grooved Roll
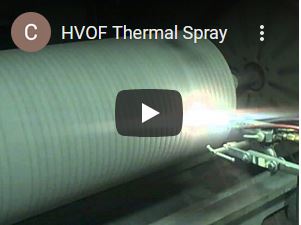
HVOF Thermal Spray Video
The HVOF (High Velocity Oxygen Fuel) coating process combines supersonic particle impact on the substrate with controlled heat energy to produce a consistent hard-particle surface distribution with high bond strengths, low porosity, and high wear resistance.
Get a quote on the HVOF and thermal spray coating services you need, or call us today at 330-551-5077. Hannecard – ASB is your trusted source for high-quality HVOF coating services.
Why Choose Hannecard – ASB for Your HVOF Coating Needs?
Hannecard - ASB consistently delivers the highest quality HVOF surfacing solutions to prolong life and improve the quality of your parts and products. We offer proven experience in liquid- and gas-fueled thermal sprays to every HVOF coating project. We are equipped to produce consistent applications of HVOF tungsten carbide or other HVOF surface coatings over a wide range of part configurations, adapting specialized masking and manipulators as needed.
What are HVOF Coatings?
HVOF thermal spray coatings utilize a mix of ignited fuel and oxygen to improve or restore a metal’s surface. HVOF coatings increase corrosion protection, erosion, and wear resistance, producing parts with dense coatings, low porosity, and high bond strength.
With many years of experience and a skilled team of thermal spray operators, Hannecard - ASB consistently delivers the highest quality HVOF surfacing solutions to prolong life and improve the quality of your parts and products.
How are HVOF Coatings Applied?
HVOF thermal spray coatings have an extremely high temperature and pressure, which is applied through a spray nozzle at ultra-high speeds. Powder is then injected into the high-velocity gas stream, which partially melts as it is applied to the part surface.
What are the Advantages of HVOF Coating Processes?
HVOF thermal spray coatings provide numerous advantages to enhance surface quality for your part or component. HVOF coating benefits include:
- Higher density
- Increased bond strength
- Lower oxide content
- Smoother surface
- Enhanced corrosion protection
- Improved wear resistance
HVOF Coating Applications
HVOF coatings protect metal substrates in various applications that require enhanced protective qualities. HVOF coating is used to protect the following applications:
- Aerospace operations
- Paper production equipment
- Petrochemical industries
- Metal coil coating
- OEM equipment
- Repair work
Custom Engineered HVOF Coating Chemistry Options
In addition to commercially available materials, we can provide metallography laboratory services to determine the best specially engineered chemistries for your specific HVOF thermal spray coating applications. Hannecard - ASB offers a range of HVOF coating options, including:
- Sprayed gripping surfaces
- Highly polished diamond grinding
- Super finishing
Additional coating options include HVOF tungsten carbide coatings and tungsten and chrome carbide coatings.
Choose Hannecard – ASB for Your HVOF Coating Needs
Hannecard – ASB is your trusted source for precision HVOF coating services. Contact us to learn more about our HVOF coating technology, services, and support, or request a quote to begin your project. A highly trained, expert representative will contact you to discuss your HVOF coating treatment options.